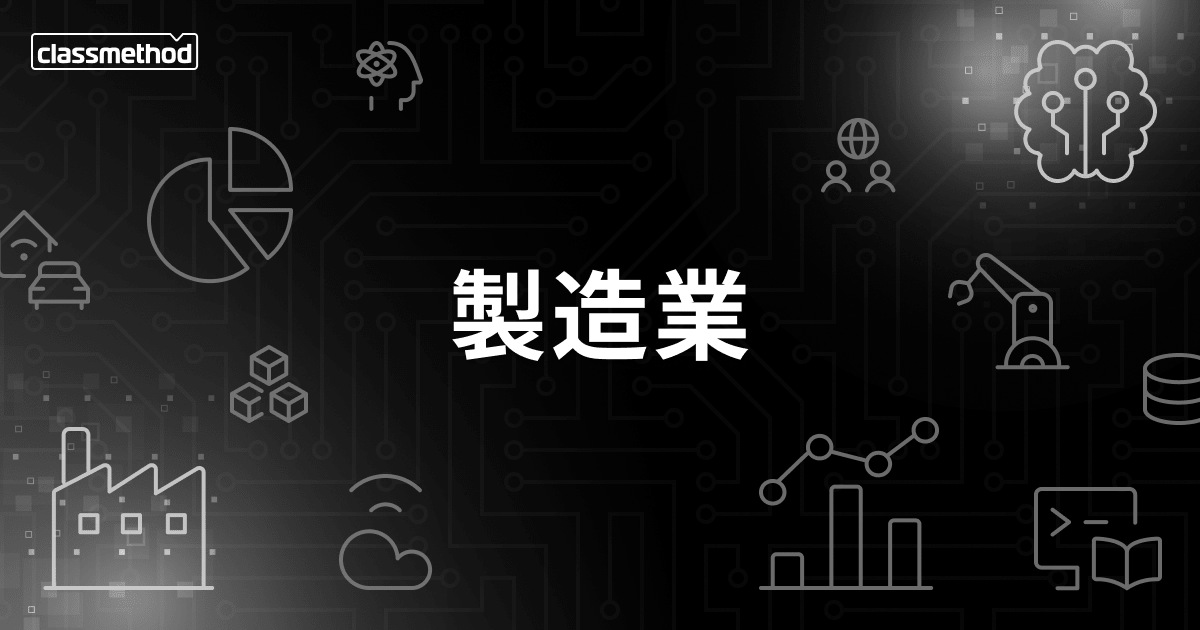
製造業DXは技術ではなく、現場から始まる
こんにちは、おおはしりきたけです。
当エントリは クラスメソッド発 製造業 Advent Calendar 2024の24日目のエントリです。
今期(21期)から、私は製造業向けにシステム開発などを行う部門を担当しております。製造業DXについての現状などは、経済産業省、総務省、IPAなどから、デジタル化の取り組みやDXの動向などまとめられておりますが、本記事ではここ数年製造業向けに取り組んできた実態を含め、リアルな現場の製造業のDXの取り組みについてもまとめていきたいと思います。
はじめに
製造業は、今、かつてない変革の時代を迎えています。市場環境の急速な変化やグローバル競争の激化により、「現場の効率化」や「データ活用」は経営において避けて通れない最重要課題となっています。最終的なゴールは、単なるコスト削減や効率化だけでなく、競争優位性を築き、事業に価値ある結果をもたらすことです。しかし、このゴールに一足飛びで到達することは不可能です。デジタルトランスフォーメーション(以下DX)は一夜にして実現するものではなく、長期的な視点と計画的なアプローチが必要です。
クラスメソッドにも、経営課題という上段の抽象度の高いご相談をいただく一方で、「まずは現場のライン一つから改善したい」という非常に具体的な声をいただくことも多くあります。これこそが、DXを推進する上での現実的な第一歩の重要性を物語っています。
DXを成功させるためには、まずは大きなゴールを明確に描くことが必要です。例えば、「生産性を30%向上させる」や「データ活用で品質トラブルをゼロにする」といった具体的かつ測定可能な目標を設定します。一方で、この目標に向かうためには、現場の課題を一つずつ解決していくという「小さな一歩」を積み重ねることが欠かせません。
例えば、あるお客様では、IoTセンサーを導入して生産ラインの稼働データを収集することからスタートしました。この小さな一歩により、特定の時間帯における稼働効率の低下が可視化され、その原因を特定して改善につなげることができました。このように、まずは手が届く範囲の課題を解決することで、DXの成功に向けた基盤が着実に築かれていきます。
DXはマラソンに似ています。一気にゴールに向かうのではなく、一歩一歩着実に進むことが、最終的に大きな成果を生みます。本記事では、この「大きなゴール」と「小さな一歩」をどう具体化し、実現していくかを解説していきます。
1.製造業のDX動向
製造業におけるDXは、競争力強化や生産性向上の鍵として注目されています。まずは、IPAのDX白書2021とDX動向2024から、製造業のDX取り組み状況を見てみましょう。
「部署ごとに個別でDXに取組んでいる」まで含めた場合、2021年は「58.9%」でしたが、2024年では「77%」まで上昇しています。全体的に「18.1%」の上昇ですが、さらに「全社戦略に基づき、全社的にDXに取組んでいる」に多いては、約20%から約40%まで上がっており、倍になっています。
この数字を見ても、ここ数年で製造業においてもDXの取り組みが、全社戦略になってきていることがわかります。
クラスメソッドで製造業のDX支援を行っているという認知は、まだまだ少ないですが、クラウド利用/移行の観点から、数年前と比べ、製造業のお客様からの問い合わせは、3倍程度増えています。
2.大きなゴールを描く
製造業におけるDXの成功には、まず「大きなゴール」を描くことが欠かせません。このゴールは、単なる技術導入を超えて、企業全体のビジョンや経営戦略と直結するものである必要があります。DXはあくまで手段であり、目指すべきは競争優位性の確立や新たな価値創造です。
なぜ大きなゴールが必要なのか?
大きなゴールは、DXの方向性を全社的に共有し、取り組みを加速させるための指針となります。これが曖昧だと、各部門がバラバラの方向を向き、せっかくの技術やリソースが無駄になってしまいます。たとえば、経営層が「全社的なデータ活用による意思決定の迅速化」を目指す場合、現場でも「生産データをリアルタイムで可視化する」など、具体的な目標が設定されます。このように、全社で共有可能な大きなゴールがあることで、部門間の連携もスムーズになります。
DXのゴール設定例
具体的なゴールを設定することで、DXの成果が明確になります。以下は、製造業で考えられるDXゴールの例です。
• 生産性の向上:製造プロセスの効率化により、生産量を20%増加させる。
• 不良率の削減:AIを活用した品質管理で、不良率を50%削減する。
• リードタイムの短縮:サプライチェーン全体をデジタル化し、製品のリードタイムを30%短縮する。
• 持続可能性の向上:エネルギー消費を25%削減し、CO2排出量を削減する。
以下の図は、「マニュファクチャリングに関する各チェーンと業務システムの連携イメージ」です。
参照: 2024年版ものづくり白書 第5章 製造業の「稼ぐ力」の向上 第2節 DXによる製造機能の全体最適と事業機会の拡大
私の部門である製造ビジネステクノロジー部では、特にPLM(Product Lifecycle Management)における、生産性の向上や不良率の削減、リードタイムの短縮といった要望をいただくことが多いです。ただ、前述した通り、一足飛びに課題の解決はできません。このように明確な目標が定義されていることで、一つ一つの小さな課題解決は何のためにやっているのか?と迷わずに済みます。
経営層と現場の目線を合わせる
大きなゴールを描くには、経営層のリーダーシップと現場の協力が不可欠です。経営層は、企業の長期的なビジョンと目標を示し、現場に必要なリソースを提供する責任があります。一方で、現場の声をしっかりと吸い上げ、現実的な課題に即したゴール設定を行うことも重要です。
たとえば、経営層が「製造工程の完全自動化」という野心的なゴールを掲げた場合でも、現場からは「段階的にセンサーを導入し、まずは可視化から始めたい」といった具体的な提案が上がることがあります。このような対話を通じて、両者の目線を合わせることで、実現可能かつ成果の出やすいゴールを設定することができます。
経営と現場を合わせるのが一番難しいところではありますが、実際のところ「経営」、「IT」、「OT(Operational Technology)」がしっかりと連携されていることが大切ですが、実態としてはかなり難しい部分もあります。あまりにも規模が大きいと計画だけ立てるのに1年以上かかってしまうこともありますので、細かい部分は変化もするので、まずは漠然とした方向性だけ合わせておくことができれば、最初の一歩は踏み出せるのではないかと思います。
ゴールは進化する
DXのゴールは、時代や技術進化、経営環境の変化に応じて進化していくものです。最初は小さな目標から始めても、達成したら次の段階へとステップアップすることが重要です。たとえば、データ可視化が完了したら、次はAIを用いた予測や最適化に進むといったように、ゴールを進化させることでDXを持続的に推進できます。
3. 小さな一歩から始める
製造業DXを成功させるには、最初に大規模な変革を目指すのではなく、現場の課題に真正面から向き合い、小さな一歩から始めることが重要です。特にシステムや技術を提供するベンダーにとっては、「まず現場に行く」 ことが最優先です。現場を知らずして、効果的な解決策を提案することはできません。
現場を見ることから始める
製造業の現場は、経営層が見ている課題とは異なる、現実的で具体的な問題が山積しています。百聞は一見にしかずです。ミーティングを何回もこなすよりも、私の考えは、「まずは現場を見させていただく」です。例えば、機械の稼働率が低下している背景には、人員配置の課題や特定の時間帯に集中するメンテナンス作業など、現場特有の事情があることがよくあります。同じ工場でもラインが違うと課題も違うことは多々あります。
ベンダーが最初に行うべきは、システムの提案や技術の導入ではなく、現場に足を運び、現場の作業環境や従業員の動き、さらには現場で使われている既存のデータ管理方法を直接観察することです。この「現場を見る」ステップを踏むことで、本当の課題を把握し、それに対する最適な解決策を設計できます。
現場主導のスモールスタート
現場の課題を把握したら、次に行うべきは小さな改善から始めることです。例えば、IoTセンサーを導入して特定の生産ラインの稼働データを可視化する、またはエクセルで管理されているデータを簡易なダッシュボードにまとめるなど、現場で即効性のある施策を試します。
現場に寄り添う重要性
現場に行き、現場の声を聞き、その課題に即した解決策を提示することは、単にシステムを提供する以上の価値を生みます。現場の従業員が「このシステムは自分たちのためにある」と感じてもらうことで、DXへの理解と協力が深まり、結果的にプロジェクトの成功率が向上します。
ベンダーは現場に足を運び、机上で設計したアイデアではなく、現場で得たリアルな課題感をもとに提案を作るべきです。「現場の課題を解決することが、DXの第一歩」という認識を持ち、現場との信頼関係を築くことが成功の鍵です。
現場での変化に対応するアジャイルなアプローチ
製造業DXのプロジェクトを進める中で、現場の状況や課題は時間とともに変化していきます。そのため、最初に設定したゴールや課題の優先順位も、プロジェクトが進むにつれて調整が必要になることが少なくありません。これを受けて顧客もベンダーも重要視すべきなのは、「現場の変化を敏感に察知し、柔軟に対応する姿勢」です。ここでアジャイルの考え方が非常に有効です。
- 現場と継続的にコミュニケーションを取る
- プロジェクトの進捗に応じて現場を訪れ、課題の変化や新たなニーズを把握します。
- 成果を小さくでも早く届ける
- 完成を待つのではなく、短期間で現場に価値を提供できる仕組みを繰り返し導入します。
- 計画変更を恐れない
- 初期の計画から軌道修正が必要になった場合でも、現場のニーズに合わせて柔軟に対応します。
4.DXを進めるステップ
製造業DXを成功させるには、現場の課題に対応する「小さな一歩」から始め、それを全社規模でスケールアップしていくプロセスが重要です。DXは一部門や一部プロセスだけで完結するものではなく、全社的な視点でデータやシステムを活用し、新たな価値を創出することを目指します。
ただ、どこから手をつけて行けばいいのか分からない製造業の方もいると思います。その場合DXの前のデジタライゼーションに取り組んでいくことから始めていくのも良いと思います。
デジタル化の取り組み4段階
経済産業省の「DX 支援ガイダンス」には、デジタル化の取り組みとして4段階に分けられています。
- ① デジタル化が全く未着手の段階 (段階 1)
- いまだに紙や電話のような口頭による業務が中心で、従来のアナログな状況の中で業務 が進められており、デジタル化が図られていない状態。
- 例えば、受発注を FAX や電話のみで実施する、勤怠管理として出勤簿に判子を押印して いる状態。
- ② デジタイゼーションの段階 (段階 2)
- 従来のアナログな状況から、デジタルツールを利用した業務環境へ移行しており、業務標 準化や業務効率化による、事務負担の軽減やコスト削減といった効果が表れはじめる状 態。
- 例えば、顧客との連絡手段であれば、従来では FAX を利用しているところを、電子メール の利用に切り替えるといった取組。
- ③ デジタライゼーションの段階 (段階 3)
- デジタルツールやインフラを活用することで、更なる業務効率化によるコスト削減や、新たな効果として、データ利活用による業務改善を実現することができている状態。
- 例えば、職人技術のデータ化、在庫情報システムによる在庫量の管理や適切な発注量 の管理、顧客管理システムによる効率的な営業活動の促進等。
- ④ DX の段階 (段階 4)
- 業務レベルを超え、デジタル化によるビジネスモデルの変革や競争力強化に取り組み、 企業の「トランスフォーメーション」を進めている状態。
- 例えば、蓄積されたデータを活用した販路拡大や新商品の開発による付加価値の向上、 自社の経営改善のために開発したデジタルツールの外販による新事業の創出等
参照:経済産業省 DX 支援ガイダンス- デジタル化から始める中堅・中小企業等の伴走支援アプローチ -
生成AIの活用
クラスメソッドの例で言うと、②のデジタイゼーションの段階で、社内からの問い合わせを生成AIとRAG(検索拡張生成)を使って、チャットボットでの問い合わせの対応を行ったりしています。
RAG(Retrieval Augmented Generation)は、大規模言語モデル(LLM)の回答精度を向上させる技術で、外部データを活用して必要な情報を補う仕組みです。この技術を使うことで、LLMをゼロから学習し直すことなく、既存のデータを低コストで活用できるため、ビジネスシーンで広く利用されています。
以下の事例は、製造業のお客様事例ではないですが、生成AIを活用して社内ナレッジを検索できるようにした事例になります。製造業のお客様では、機器のマニュアルなどを生成AIを活用して検索できるようにしてたりもします。
可視化から始めても良い
DXを推進する際、多くの製造業が直面する課題は、「何から手をつけて良いかわからない」という点です。そのような場合、最初のステップとして「可視化」から始めることが効果的です。データの可視化は、現場で起きていることを「見える化」し、課題や改善ポイントを具体的に把握するための重要な一歩です。
なぜ可視化がDXの第1歩に適しているのでしょうか?
- 現場の課題が浮き彫りになる
- 可視化は、現場で見えにくい問題を発見するための手段です。例えば、製造ラインの稼働データやエネルギー消費量、不良品発生率などをリアルタイムで可視化することで、どの部分が効率を下げているか、どの工程で改善が必要かが明確になります。
- 現場と経営層の共通認識を生む
- データが可視化されることで、現場の状況を経営層にも共有しやすくなります。「現場ではこうなっている」「数字としてこれが問題だ」と具体的に伝えられるため、全社的な理解と協力が得やすくなります。
- 大きな投資をせずに始められる
- 可視化はIoTセンサーや既存のエクセルデータなど、小規模なツールから始められるため、大きなリスクを取らずに進めることができます。
弊社でも、まずは簡単に工場機器(PLC)の可視化が行えるソリューションがあり、こちらを活用してから徐々に始めていくお客様も増えておいます。
可視化は、DXの第一歩として最適なアプローチです。小さな改善を積み重ねることで、現場に信頼感を生み出し、次のステップであるデータ分析やプロセス改善、さらには全社的なDX展開への道筋を築くことができます。DXを「どこから始めるべきか」に悩んだ際は、まず現場を見える化することからスタートしましょう。
5.製造業DXがもたらす未来
まだまだ、我々は製造業DXに向けて道半ばですが、製造業DXは、単なる業務効率化やコスト削減にとどまらず、製造業の未来を形作る力を持っています。ここまで、動向、大きなゴールの描き方、小さな一歩の重要性、どこからアプローチすると良いかを、弊社の現状を踏まえて書かせていただきました。最後に、製造業DXを推進することで得られる未来像のイメージ、そして、どのように製造業を進化させるのかを考えてみます。
競争力強化と新たな価値創造
製造業DXを成功させることで、製造業はこれまでにない競争力を手にすることができます。たとえば、以下のような進化が期待されます。
- 生産プロセスの最適化
- データ分析やAIの活用により、生産ラインの稼働効率を最大化し、不良品率を削減する。予測メンテナンスの導入でダウンタイムを最小化し、安定した生産体制を構築。
- 顧客価値の向上
- 製品単体の提供から、サービスやサポートを含むソリューション提供型のビジネスモデルへの転換。顧客ごとのニーズに応じたカスタマイズ製品やサブスクリプションサービスの提供が可能になります。
- 持続可能な製造
- 資源効率やエネルギー消費を最適化し、環境負荷を削減。持続可能性を重視する企業としての社会的評価を高め、新しい市場機会を創出することができます。
製造業の枠を超えた変革
製造業DXは、製造業そのものを進化させるだけでなく、業界全体や関連産業との連携を強化し、エコシステム全体を変革する可能性を秘めています。ここまでたどり着くのには数十年かかるかもしれませが、日本を盛り上げていくためには、業界間の連携も重要だと考えています。
- サプライチェーン全体の透明性向上
- データのリアルタイム共有により、サプライチェーン全体の効率を向上。リードタイムの短縮やコスト削減を実現できます。
- 新しいイノベーションの創出
- デジタル技術を活用することで、他業界との連携や新しい事業機会が生まれる。たとえば、製造プロセスで蓄積したデータを外販し、新たな収益源を確立するケースもあります。
さいごに
製造業DXが進む中で、AIやロボット、IoTなどの先端技術が注目されがちですが、製造業において人間の役割は依然として非常に重要です。技術と人の融合こそが大切だと考えています。技術はDXを加速させるエンジンであり、人はその方向性を決める舵取り役です。両者が補完し合うことで、効率性だけでなく柔軟性やイノベーションも生まれます。製造業の未来を切り拓くには、最先端の技術を活用しながら、人材を育て、活かすことが何よりも重要です。
そのためには、製造業DXを進めるために、ITや技術の導入を目的とするのではなく、現場の課題を解決し、組織全体の価値を高めるプロセスが大切です。そして、その中心にあるのは、現場を理解し、課題に向き合う「人」の力です。デジタル技術は、その「人」の力を補完し、最大化するための手段でしかありません。だからこそ、現場を見ること、人を育てることをDXの基盤に据え、着実に一歩ずつ進めていくことが、成功への道を切り拓くのです。
「製造業DXは技術ではなく、現場から始まる」。この意識を持って、一歩を踏み出しましょう。